General
|
|
|
|
|
Kason Products
|
|
|
|
|
|
|
|
|
|
K-Tron Products
|
|
|
|
|
|
|
Sturtevant Products
|
|
|
|
|
|
|
|
|
|
Western States
|
|
|
|
|
|
|
|
|
Abanaki Products
|
|
|
|
|
Technical Article Reprints:
Process Automation with Feeding, Pneumatic Conveying, and Systems Engineering
Click one of the links below to read or download any of these articles. These are PDF files and require Adobe Acrobat Reader.
|
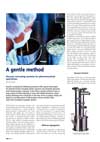
|
A Gentle Method: Vacuum Conveying Systems for Pharmaceutical Operations
CPP - 2 Pages
Vacuum conveying for tabletting operations offers special advantages for material transfer including cleaner, dust free and contained operation with minimal product exposure. It also offers a gentle method to move a large volume of bulks especially in areas with height limitations, where gravity discharge from a large bin or tote may not be an option. Finally, the option to use either dense or dilute phase vacuum transfer offers much more versatility in powder transfer.
|
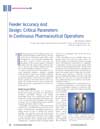
|
Feeder Accuracy And Design:
Critical Parameters In Continuous Pharmaceutical Operations
Pharmaceutical Solutions Update: Pharmaceutical Online
3 Pages
The manufacturing sector of the pharmaceutical industry is currently undergoing a radical change. The need to improve process and product quality while controlling overall process costs is growing. Continuous processing offers a chance to achieve these goals. The implementation of PAT (Process Analytical Technology) tools further aids in the support of the continuous operation, as the tools give real-time indication and assurance of product quality throughout the process. A variety of batch processes in the industry are currently undergoing continuous evaluation, including continuous direct compression or blending, continuous wet and dry granulation, and continuous granulation via hot-melt extrusion. At the heart of each of these continuous operations is the feeder which is used to proportion raw ingredients into the process. Feeder technology and accuracy is paramount in the overall continuous process.
|
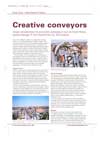 |
Creative Conveyors: Design Considerations for Pneumatic Conveying of Coal
Solids & Bulk Handling - 2 Pages
If you ask six different engineers for a pneumatic conveying system, you will likely get at least six different designs. This case study shows how a few of the applied concepts worked in an actual installation and the reasoning for the approach. The overview includes helpful hints and insights behind the decisionmaking process concerning convey line construction, filtration, storage, and temperature as it affects a dilute phase conveying system. Although the material being handled in this case is coal, the principles can be applied to many other materials. The story began with a coal processor who incorporated a dilute phase pneumatic conveying system into its production. A wide variety of coal is delivered via railcar, crushed and dried before it is introduced into the pneumatic conveying system at ambient temperatures. The material is then stored, processed and pneumatically conveyed once again, but at elevated temperatures. The final product is formed into billets.
|
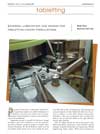
|
External Lubrication: One Remedy for Tabletting Finicky Formulations
Tablets & Capsules -
Pharmaceutical formulators traditionally blend lubricants like magnesium stearate into tablet formulations to aid flowability and lubricate tablet press tooling. Depending on the formulation, however, internal lubrication can be problematic. Magnesium stearate is typically the lubricant, though not always, and it has a tendency to coat the particles,” said James Mossop, technical products manager, Fette America, Rockaway, NJ. “If you blend too much, you can over-blend, which means you’re over-coating the particles. That has an effect on dissolution, and sometimes on content uniformity. It also hinders the ability for the particles to adhere to each other during compression. Typically, it takes more compression force to make them bind so you can form the tablets to the right thickness and the right hardness.
|
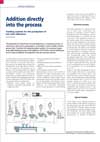
|
Addition Directly into the Process:
Feeding Systems for the Production of Hot Melt Adhesives
CPP - 2 Pages
The production of solvent-free hot melt adhesives is a continuous process. In most cases a twin-screw compounder or co-kneader is used to obtain a homogenous melt. To achieve the required product quality, it is necessary to guarantee high feeding accuracy of the additives. K-Tron offers various feeding systems for precise addition of components into the extrusion process. Hot melt adhesives are solvent-free. They are characteristically solid at temperatures below 82 °C, melt into low-viscosity fluids above this point and set rapidly upon cooling. The development of hot melt adhesive technology was inspired by the previous use of molten wax for bonding. When this method no longer satisfied performance needs, 100 % thermoplastic systems were introduced. Today, there are many different hot melt adhesives available in the marketplace, the most common being those used for hot melt, pressure-sensitive adhesive applications.
|
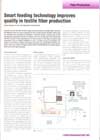 |
Smart Feeding Technology Improves Quality in Textile Fiber Production
Chemical Fibers International - 2 Pages
Typically the production of man-made colored textile and carpet fibers involves the feeding of two or more components into a single screw extruder, where they are blended and extruded as a filament. Filament pumps, nozzles and further processing equipment ensure the fibers have the correct form and thickness. The key concern of the manufacturer is that the color of the fiber is uniform and consistent, with no visible variations in color. In order to ensure consistent coloration of the fibers modern processes generally use gravimetric feeding systems, which can feed the highly concentrated masterbatches in various granulate forms with high accuracy.
|
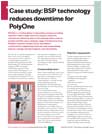
|
Bulk Solids Pump (BSP) Technology Reduces Downtime for PolyOne
Plastics, Additives and Compounding - 4 Pages
PolyOne is a leading global compounding company, providing customers with a single source for polymer, elastomer, colorant and additive products. The company offers a diverse product portfolio and a complete range of technical services. PolyOne's business includes color and additive masterbatches, engineering materials, vinyl compounding, polymer coatings and thermoplastic resin distribution. This article examines how the K-Tron Bulk Solids Pump integrated into the K4G Gravimetric Blender reduced downtime for PolyOne.
|
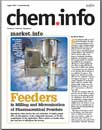
|
Feeders in Milling and Micronization of Pharmaceutical Powders
Chem. info - 2 Pages
Operations often involve the size reduction of highly potent API's. As the potency of the dry compounds increases, so do the complexities of the application. This article offers advice in feeder selection and how it influences the process. Size reduction mills are used widely throughout the pharmaceutical industry for the reduction of active pharmaceutical ingredients (API's) as well as bulk pharmaceuticals and excipients such as lactose and hydroxypropylmethyl cellulose. Size reduction is used to increase surface area, improve formulation dissolution properties and maintain a consistent average particle size distribution (PSD) for the formulation, allowing for a better quality mixture when creating solid dosage forms suce as tablets and capsules.
|
|
Vacuum Conveying of Powder (In sanitary and non-sanitary applicaitons)
Solids & Bulk Handling - 2 Pages
Moving powders from one place to another can be a tricky business with all the regulations regarding hygiene, hazardous locations, cleanliness and safety to be adhered to. If the transfer process can be combined with a secondary process, then savings can be enormous in both manpower and wastage. Vacuum conveying allows powders to be moved with the addition of other crucial process steps. Roger Burgess of K-Tron PCS GB, Stockport UK, looks at the flexible, hygienic and economic benefits of vacuum conveying.
|
|
Plastic Compounder Finds K-Tron Quick Change Feeders Meet the Challenge for Short, Customized Runs
Powder and Bulk Engineering - 1 Page
A plastics compounding company in South East Asia recently took on the challenge of also offering a variety of engineering plastics, producing custom colors and other customized additives. The business of customizing colors and other additives to specific customer needs required Just-in-time (JIT) delivery and multiple short runs. They were looking at the huge task of making numerous product changes a day throughout the plant.
|
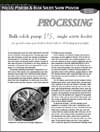
|
Bulk Solids Pump vs. Single Screw Feeder: An Up-and-Comer goes Head-to-Head with an Old Feeding Heavyweight
Processing Magazine - 2 pages
Over the years, just four feeding technologies have emerged as leading methods for controlling feeder flow rate. The screw/auger, belt, rotary valve and vibratory feeders account for more than 90 percent of all feeders in use today, whether volumetric or gravimetric. But demanding performance requirements in hi-tech sectors of the plastics, food, pharmaceutical and other industries have brought feeding technology under critical scrutiny, leading to a new design, the Bulk Solids Pump (BSP). In laboratory tests comparing the BSP and a single screw feeder, the exceptional uniformity of the BSP's discharge contrasts sharply with the single screw's pulsation, as clearly revealed in one-second samples.
|
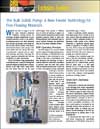
|
The Bulk Solids Pump: A New Feeder Technology for Free-Flowing Materials
Powder Bulk Solids - 3 pages
While the screw auger is by far the most commonly employed volumetric feeding device, increasingly stringent requirements in performance- intensive sectors of the plastics, food/pharmaceutical and other industries have brought this popular screw feeder under scrutiny. These performance concerns include short term discharge uniformity, full range linearity, long-term calibration drift and fast cleanability for quick turnarounds.
|
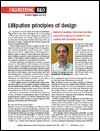
|
Lilliputian Principles of Design
Engineering R&D - 2 pages
Scalability is a two-way street, and there are engineering hurdles to clear when reducing the size of a processing unit, just as there are when enlarging one. Engineers at K-Tron International, Inc.'s Process Group faced the former scenario when developing the Bulk Solids Pump (BSP), an alternative to augers, weigh belts and vibratory trays in the transfer of granular materials.
|
|
Smart Refill Technology in Loss-in-Weight Feeding:
How to Enhance Loss-in-Weight Performance in Higher Rate Refills
Processing Magazine - 4 pages
Weighing and control advancements over the years have made loss-in-weight (gravimetric) feeding the preferred method wherever the combination of high gravimetric accuracy, ingredient containment, and material handling capability are needed. However, loss-in-weight feeding does possess some shortcomings, especially at higher feed rates. Feeder companies have taken varying approaches to the challenges present during refill of the feeder's hopper. One company, K-Tron, utilizes an approach called "Smart Refill Technology" (SRT). Smart Refill Technology ensures that intermediate to high rate loss-in-weight systems do not have to suffer from feed rate inaccuracy during refill and can use a more compact hopper offering a more economic solution to fitting into tight locations in the factory.
|
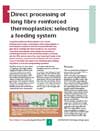
|
Direct Processing of Long Fibre Reinforced Thermoplastics:
Selecting a Feeding System
Plastics Additives & Compounding - 4 pages
Long fibre-reinforced thermoplastics are a recent development in newer technologies where polypropylene or thermoplastic material is directly compounded with long glass fibres (rovings) and then moulded in one operation. Long fibre thermoplastic technologies are currently of considerable interest in the automotive industry in Europe and the USA and are one of the most important trends in the plastics industry at present.Alfred Häuptli of K-Tron explains some of the issues that need to be considered when feeding long fibres in an in-line compounding operation.
|
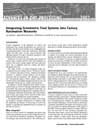
|
Advances in Dry Processing: Integrating Gravimetric Feed Systems Into Factory Automation Networks
Powder / Bulk Solids - 6 pages
Systems integration, or the integration of controls and instruments from various manufacturers into process control lines, has always been a challenging area of engineering practice. Except for certain legacy systems and the lowest level interfaces to actuators and sensors, analog signals and relay logic have given way to industrial serial bus systems and factory automation networks. This paper focuses on systems integration issues surrounding gravimetric feeding controls. Gravimetric feeders are a common component of many continuous production processes in chemical, plastic and food processes.
|
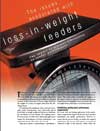
|
The Issues Associated with Loss-in-Weight Feeding: The Impact of Process Timescales on Feeder Performance
Processing Powder Handling Handbook - 4 pages
The purpose of a bulk solids feeder is simply to discharge material at a controlled rate. How well a feeder fulfills this purpose is primarily reflected in its repeatability performance. Repeatability is a statistical measure of the consistency of feeder output based on the weights of a series of samples taken from the discharge stream. This article strives to sensitize the engineer to the impact of process timescales on feeder performance requirements, and highlights issues associated with loss-in-weight feeder performance over brief intervals.
|

|
How to Troubleshoot and Maintain Your Feeder
Powder and Bulk Engineering - 4 pages
Troubleshooting and maintaining your feeder to ensure that it meters material accurately and efficiently to your process depends on a solid understanding of how your feeder operates. After explaining how three common feeders operate, this article gives advice on how you can troubleshoot and maintain each of the feeders.
|
|